The Payoff From Teamwork
Business Week - July 10, 1989 - By John Hoerr
The Gains In Quality Are Substantial - So Why Isn't It Spreading Faster?
What the company wants is for us to work like the Japanese. Euerybody go out and do jumping jacks in the morrning and kiss eack other when they go home at night. Yon work as a team, rat on each other, and IQse control of your destiny. That's not going to work in this country --John Brodie, President United Paperworkers Local 448 Chester, Pa.
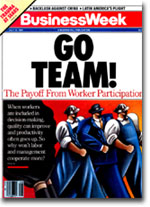 |
This article was featured in Business Week. |
Call it employee involvement (El) or worker participation or labor-management "jointness," as it is now known in the auto industry. Whatever the term, the concept is clearly troubling for many Americans. At one and the same time, it promises workers autonomy over their jobs but also threatens their old ways of working. It gives managers a powerful tool to improve produetivity and quality but could undermine their control. EI may be American.industry's best hope of competing with the Japanese and Europeans, as well as lowwage, Third World producers. Yet for years, timid U. S. companies have merely sloshed a thin coating of El across an aging industrial base.
But now, there are signs that real employee involvement is sinking into the core of Corporate America. While angry union officers such as the Paperworkers) Brodie still rail against participation, more and more workers and labor leaders are willing to risk EI in hopes of making their employers more competitivc and their jobs more secure. This message came across strongly at the recent United Auto Workers convention in Anaheim, Calif. In one of the most raucous debates in UAW history, critics made the rafters ring with charges that "jointness" consisted of little more than "co-optation" and a new form of the ageold `'speedup." But delegates favoring cooperation overwhelmingly voted down the dissidents. And when the meeting ended on June 23, the UAW's leaders were more strongly committed than ever to EI programs at the Big Three automakers.
The UAW'S approval will make it easier for other unions to give more than lip service to EI. And there are comparable changes in management attitudes. So what had been a slow evolution of E] iS turning into a revolution in the way work is organized and managed in the U. S. Companies that only a few years ago disdained participation are rushing to set up so-called self-managing work teams, the most advanced stage of El (table). The team concept is spreading rapidly in industries such as autos, aerospace, electrical equipment, electronics, food processing, paper, steel, and even financial services.
Although work teams differ from company to company, they typically consist of 5 to 12 multiskilled workers who rotate jobs and produce an entire product or service with only minimal supervision. Adopting the team approach is no small matter; it means wiping out tiers of managers and tearing down bureaucratic barriers between departments. Yet companies are willing to undertake such radical changes to gain workers' knowledge and commitment - alone with productivity gains that exceed some cases.
Despite these recent signs of ET'S growing acceptance, many workplace experts believe it is not spreading fast enough. "Participation is growing, but at an alarmingly slow rate considering the quality and productivity payouts," says Jerome M. Rosow, president of the Work in America Institute, a nonprofit research group that advocates employee involvement. He and others believe that the federal government now should actively promote El. "We'll see some incremental growth in participation but not widespread diffusion unless it gets reinforeed in public policy," says Thomas A. Kochan, a professor at Massachusetts Institute of Technology who has studied the E] movement for more than 10 years.
Resistance to further EI growth remains widespread. Many managers won't allow participation because it entails sharing power with employees. Low-level supervisors, whose interests often are ignored in the EI process, tend to fight it. For participation to become a way of life in industry, it also must overeome Wall Street's insistence on shortterm results. Managers who fear hostile takeovers think twice about investing in human-capital programs such as the continual training that's needed to help workers improve their technical and social skills. "Very few companies understand how deep the change must be, and really go after it," says W. Patriek Dolan, a St. Louis consultant who works with unions and employers on E! programs. "Training is always a peripheral, secondary consideration, and when push comes to shove, it keeps sliding."
Quality Circles
Although unions are declining in power, they still represent 24% of workers in the crucial manufacturing sector. Without their assent and help, instituting work reforms to boost efficiency simply is not possible. But many union leaders, veterans of a decade when management fought hard to avoid, oust, and beat down organized labor, are suspicious. Militant unionists see management proposals for work teams as unionbusting ploys-and sometimes they are. Even union presidents who strongly advocate El, such as Lynn R. Williams of the United Steelworkers, can't force their philosophy on local officers. At Inland Steel Co., for example, Mike Mezo, president of the 10,000 member usw Local 1010, flatly declares: "We don't think there's any benefit to cooperation. No way will we ever take part."
Despite this opposition, a broad array of employers practice some form of participation. Government employees are involved in El efforts at~ many agencies, including the U. S. Postal Service and the New York City Sanitation Dept. Workers at the Philadelphia Zoo suggest ways to draw more visitors, and they get bonuses when attendance rises. A 1987 survey by the U. S. General Accounting Office found that 70~ of 476 large companies had installed the most common EI form, problem-solving committees usually known as quality circles (QCS). But the coverage was spotty. At 70% of the companies studied, less than half of the work force was involved in EI activities.
A Voice
But that constituted some progress over the 1970s, when the participation movement clung precariously to life at a few dozen leading-edge companies. Starting about 10 years ago, the trumpeting of Japan's success with participation induced hundreds of U.S. companies to copy the Japanese approach in setting up QCS. Recommendations made by quality circles can improve quality and cut costs. But Q&s are merely "offline" discussion groups and don't reorganize work or enlarge the role of workers in the production process.
Since the mid-1980s, however, participatory methods have advanced far beyond mere problem-solving teeLniques copied from the Japanese. It's at this point that American practices are beginning to diverge from those used in Japan. Work-reform experts say this is necessary to avoid imposing a foreign work culture on the U. S. workplace.
In American-style teamwork, for example, workers not only gain a more direct voice in shop-floor operations-as in Japan. They also take over managerial duties, such as work and vacation scheduling, ordering materials, and hiring new members. But there is no law that says this must happen, and plenty of U. S. companies install teams without corresponding participation. Increasingly, too, American union officials demand a consulting or decision-making role on plantwide issues such as production scheduling, capital expenditures, and introduction of new technology. After the A. O. Smith Corp. automotive parts plant in Milwaukee converted last year to the team approach, one proud worker, Albert Porter, exaggerated only slightly when he boasted: "They tumid over control of the shops to us."
In fact, the EI movement has unleashed enormous energy and creativity stored up by the Albert Porters who like the idea of using their brains, as well as their bodies, on the job. It increases their feelings of dignity and self-worth. Opponents of cooperat~on may get more press, but pro-E~ workers constitute a much larger portion of most work forces. Studies show that in many plants where participatory aet*ities are not mandatory an average of about 25~ of the workers volunteer to join problem-solving teams. Another 70~ are passive supporters, while only 5~ remain opposed.
This points up one of the irm nies of the E! movement. Although unions introduced the idea of "industrial democracy" early in this century, it is now management that is pushing employees in both union and nonunion plants to accept more involvement-and not to make workers happy but to improve the company's bottom line.
About Face
If the U. S. is to become a world-class manufacturing nation, companies must be able to produce in small lots, customizing products to increasing demands. This calls for flexible work practices and workers who are willing to move from job to job. Teamwork makes this possible because the employees usually are "cross-trained" to perform all tasks. They can fill in for absent co-workers and respond quickly to changes in models and production runs. A General Electric Go. plant in Salisbury, N. C., typically changes product models a dozen times a day by using a team system to produce lighting panelboards. This plant has increased productivity by a remarkable 250% compared with GE plants that produced the same products in 1985. It combines teamwork with "flexible automation" and other computerized systems.
Salisbury's success convinced even GE's typically hardheaded managers that participation can boost profits. As recently as the early 1980s, when many companies succumbed to the quality-circle fad, GE hung on to its traditional management style. But in the past few years, GE'S top management has done an about-face. Of its 120,000 U. S. employees, nearly 20~ now work under the team concept. GE doesn't dictate what human-resource practices each plant must adopt, but it encourages innovation. The corporate goal is to have 35% of the work force in teams by the end of 1989. "We're trying radically to reduce the work cycle needed to produce a product," says Robert Erskine, manager of production resources. "When you combine automation with new systems and work teams, you get a 40% to 50% improvement in productivity."
But teamwork plants are by no means workplace Utopias. For two years after &E's Salisbury plant converted to teambased production in late 1985, it had a 14% turnover rate; many workers quit rather than accept more responsibility and face constant movement from job to job. `'It's not all wonderful stuff," warns plant manager Roger Gasaway. "But we've found that when you treat people like adults, 96% act like adults." And teamwork can provide exceptional opportunities for self-development. In Salisbury's pay-for-knowledge plan, employees can raise their salaries by completing company-funded courses in technical, economic, and behavioral subjects.
The team idea is mushrooming throughout manufacturing. It's also gaining a toehold at banks, insurance firms, and other companies specializing in financial services. In Morristown, N. J., for example, AT&T Credit Corp. uses teams of employees to process applications from companies that want to lease computer equipment (box). But teamwork is rare in the service industries, which account for more than 70% of employment in the U. S. In other words, the most productive form of participation hasn't spread to many millions of employees.
Human Factor
At the same time, economists are beginning to see marked evidence of El's impact on efficiency. In a newly released report for the Brookings Institution, Steve Levine and Laura D'Andrea Tyson of the University of California reviewed all major studies of employee involvement. '`If you sum it all up, meaningful participation has a positive effect on productivity. It's almost never negative or neutral," Tyson says. Moreover, studies of employee-owned companies show that stock ownership alone doesn't motivate employees to work harder, while ownership combined with participation does.
Indeed, the "human factor" emerges as the critical element in efforts to make auto plants more competitive, according to a study of 66 plants around the world by the International Motor Vehicle Program at MIT. Plants that combined computer-based technology with advanced work innovations outperformed all others. Automated plants with no work reforms were the poorest performers. But teams are "no panacea unless they are integrated in a whole new approach to the production system," says John Paul MacDuffie, an MIT research associate.
This growing body of evidence suggests strongly that the old system of assumptions, beliefs, and practices relating to work has been disproved as a pattern for modern factory and office jobs. Based on principles developed by Frederick W. Taylor, the old paradigm involved the division of production work into simple, repetitive tasks performed by unskilled workers under close supervisory control.
Labor Warfare
In the new paradigm, workers will be multiskilled and to some degree will manage themselves through teamwork. Management will train workers, share business information with them, and develop specialized "gainsharing"-or bonus-plans to allow workers to cash in on the gains of increased productivity. Jobs will be protected by longterm security plans.
American companies are now discovering what the Japanese learned long ago: that people not technology alone or marketing ploys-are the keys to success in global competition. Indeed, American workers can be just as productive as 3apanese workers. This has been demonstrated conclusively by the success of Honda, Toyota, and Nissan using American labor in U. S. plants. The keys to Japanese competitive superiority are their management and production systems, not some unique feature in Japan's group-oriented culture.
But the growth of participation in Japan wasn't snarled by the kind of implacable labor-management warfare that exists in many U. S. industries. Moreover, the "no cooperation" slogan of diehard EI opponents is understandable to foreign labor experts such as Harno Shimada, an economics professor at Keio University in Tokyo who has studied Japanese and American labor systems. "If American unions give in to American management, they run the risk of being destroyed because management alwayswants to destroy them," he says. Japanese unions aren't threatened this way, he says.
For these reasons, militant unionists contend that management can never be trusted. In using work teams, charges Don G. Douglas, president of United Auto Workers Local 594 in Pontiac, Mich., "the company has a hidden agenda to erode the collective hargaining system, to lessen resistance to changes that are more favorable to the company than they are to the employees."
And the militants' position seems validated by hardball company tactics to force acceptance of El. For example, UAW members complain that General Motors Corp. has threatened to shut down plants unless the union accepts the team concept. In the pulp and paper industry, the United Paperworkers International Union at Mobile, Ala., and Chester, Pa., waged long-and losing- strikes in 1986 and 1987 against demands by Scott Paper Co. for contract changes that would allow establishment of work teams. The UAW's Brodie contends that the company demanded the new provision without explaining why. At both Chester and Mobile, the union caved in when Scott threatened to hire permanent replacements. Scott won these battles, but at the cost of embittering the workers. Perhaps belatedly understanding this, the company hasn't tried to force the locals to accept teamwork.
Brodie's criticism of teamwork as a Japanese import is echoed by other unionists who claim that management is really trying to "Japanize" the U. S. industrial-relations system. Actually, the work-team concept was developed and used in Britain, Sweden, and the 15. S. Iong before Japanese auto makers introduced their own, highly efficient model on a wide scale. Now that Japanese companies operate many plants in the U. S., American management and labor are beginning to see that worker participation means quite different things in the two countries. To American unionists, real participation means not only problemsolving on the shop floor but also gaining a voice in higher-level decisions.
But that is precisely what the Japanese-style team concept does not do. The "team concept is not intended to increase workers' autonomy but to help them find out the problems in the production line so that no defective goods will be produced," says Keio UniversityJs Shimada. `'In the U.S.,', he adds, "workers tend to take participation as having a voice in all kinds of things that in Japan are determined by management and engineers." The Japanese system seems to work well at their auto plants in the U. S., but most of them employ nonunion workers with few expectations about sharing power with managers.
In union auto plants, however, the method of organizing work on an assembly line is a burning issue. The UAW seems to prefer the approach that is evolving in Sweden. At two Volvo plants, teams assemble large units of a car-indeed, an entire car in the case of Volvo's new plant at Uddevalla-without much supervision at all. Some GM plants, however, are adopting the Japanese method used at New United Motors Manufacturing Inc. (NUMMI), the joint venture between GM and Toyota Motor Corp. in Fremont, Calif. Japanese-style teams work on conventionally organized lines, performing minutely subdivided tasks. Team members have a lot of discretion in improving quality, but they work under first-line supervisors.
Trust
American-style teams force significant changes in work practices, and unions are still struggling to find a new role on the shop floor in teamwork plants. With only one or two classifications for production jobs, employees have to learn a wide variety of tasks and move with the flow of work. They typically can't use their seniority, the bedrock of American unionism, to bid for better or easier jobs. In some nonunion plants, team members are expected to rate each other's performance and sometimes even fire shirkers-though most unions refuse to let their members get involved in disciplinary decisions. And teamwork also can reduce the influence of the union on traditional matters such as seniority and the grievance procedure.
"There's no question managers in Japan can get away with doing some things, because of a more compliant labor force, that would not be accepted in America," says Robert E. Cole, a U. S. authority on Japanese labor practices at the University of Michigan. But American unions can protect their members by aggressively monitoring E! programs. At A. O. Smith in Milwaukee, the president of the A. O. Smith Steelworkers Union, Paul Blackman, insisted on setting up work teams so that his members could have more influence in operations. Moreover, Blackman has a voice in all major decisions made by company officers. But it is hard to write this kind of participation into a contract, and U. S. unionists are wary of giving up one kind of power in the mere hope of gaining another.
National Strategy
Cole points out an important reason why employee involvement has spread more quickly in Japan and Sweden than in the U. S. In both countries, national organizations that promoted participation had the respect and support of top corporate management. The Japanese Union of Scientists & Engineers not only advocated the quality-circle approach but actually helped companies install QCS. In Sweden, the Employers' Federation acted as a consultant for companies introducing participation. And the powerful Swedish labor movement, which is closely allied with the dominant Social Democratic Labor Party, has pushed participation as a means of gaining a voice in corporate decisions.
No comparable organizations exist in the U. S. Nor is there a large federal presence. The Labor Dept.'s Bureau of Labor-Management Relations & Cooperative Programs gathers and disseminates information about employee involvement. But most of its $6 million annual budget must be spent on other programs. Although Sweden's work force is less than a tenth the size of America's, the government-financed Center for Working Life spends $6.5 mill~on a year on programs "to help democratize working life."
In the U. S., states such as Massachusetts, Ohio, New York, Pennsylvania, and Indiana also promote EI and provide funds and technical help to companies and unions. But as helpful as these programs are, says IIIT'S Kochan, they can't substitute for the central role that the federal government could play in building networks of professionals across the nation. What is needed, Kochan adds, is '`a statement that the government recognizes the centrality of these innovations to its long-term economic strategy." The government could encourage participation- just as it has capital investment-through a tax-credit system, Kochan says.
Alienated
Richard E. Walton, a top EI theorist at Harvard University, says participation should be at the heart of a national competitiveness strategy. This means investing in human capital, as well as technology, to boost productivity. "People must see the interrelationship between social performance and economic performance," Walton says. "To have world-class quality and costs and the ability to assimilate new technology, we must have the world's best ability to develop human capabilities."
The U. S. is moving in that direction. Participation has permanently altered the old industrial relations system, based on the idea that efficient mass-production inevitably breeds alienated workers who must be bought off with high pay. The EI movement puts the lie to that assumption. When jobs are challenging, workers are committed and perform superbly. But participation will remain only a beachhead in hostile territory- unless management, labor, and government join forces to foster the revolution in the way Americans work.