Teamworks
The Next Dimension - Fall 1989 - I/N Tek
Refining the Teambuilding Process: Benefit to I/N Tek Employees, Customers
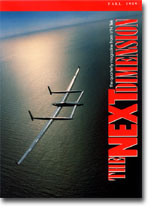 |
This article was featured in The Next Dimension. |
Steelmaking is a process of refinement. In its most basic form, it involves reducing the amount of carbon and other elements from molten iron. At I/N Tek, however, there is another refining process that goes beyond the making of durable, yet malleable metal. It extends to the plant floor, where well-coordinated teams will soon be setting their own agendas, deadlines and quality controls, to produce a steel product whose excellence, many believe, will be unsurpassed.
This team effort, which emphasizes employee participation and product quality, did not come about overnight. It came about through months of intensive preparation by some 160 employees, most of whom ventured to Japan for four to eight weeks of extensive training at Nippon Steel Corporation, whose Hirohata assembly line is the model for I/N Tek's new Continuous Cold Mill plant in New Carlisle, Indiana.
Operators and equipment-control personnel went overseas, along with a number of management resource representatives. The result, according to Rick Podkul, an I/N Tek operator, is a new sense of partnership, both between I/N Tek employees and management, and I/N Tek employees and the company's customers.
"Now I feel as if my opinions are of value," said Podkul. "You're part of a team where everyone is listened to. Everyone is given the same consideration - from top to bottom."
The training I/N Tek employees received in Japan helped foster a total team concept, reinforcing the I/N Tek corporate philosophy, which emphasizes that each employee has an equal stake in the betterment of the entire company, from the quality of its products to relations with customers. Working in 12-14 member teams, I/N Tek employees learned to rely on each other, and came to realize that both their jobs and their futures would be enhanced by working together.
"We became a tight-knit group," said John Mazany, also an I/N Tek operator. "Our training was very intense. We came away from Japan with some very strong feelings. We feel good about our jobs; we feel good about ourselves."
Added Podkul, "We can now deal with customers in a more personal way. If customers have questions about the product itself, they can deal with us as well as dealing through management." This, employees believe, results in better service to those customers, something I/N Tek management thinks will be a key ingredient to the company's long-term success.