I/N Tek And I/N Kote: A Joint Venture Built On Participation And Partnership
1992 - By Christopher B. Meek and Jason Bates
Marriot School of Management, Brigham Young University
"The research effort on which this publication is based was partially sponsored by the Air Force Office of Scientific Research, Air Force Material Command, USAF, under grant number F49620-95-1-0052, US-Japan Center of Utah, The U.S. Government is authorized to reproduce and distribute reprints for governmental purposes notwithstanding any copyright notation thereon."
Introduction
Sixteen miles east of the industrial city of South Bend, in the midst of the corm fields of the tiny rural farming community of New Carlisle, Indiana, are two of the newest and most technologically and socially advanced steelmaking operations in the world, I/N Tek and I/N Kote. Both companies are joint ventures established by a U.S. steelmaker, Inland Steel Company, and the largest and most technologically sophisticated steel producer in the world, the Nippon Steel Corporation of Japan. Together, the two operations required a massive initial capital investment of $1.1 billion. I/N Tek, a state-of-the-art continuous cold rolling mill, is 60 percent owned by Inland Steel and 40 percent owned by Nippon Steel. The formation of this joint venture was announced in March 1987. Three years later, in March 1990, the first commercial steel rolled off the line. I/N Tek provides steel to auto, office furniture, and home appliance manufactures throughout North America. The facility can produce over 1.4 million tons of cold rolled steel annually and has manufactures more than 6.2 million tons since first starting operations.
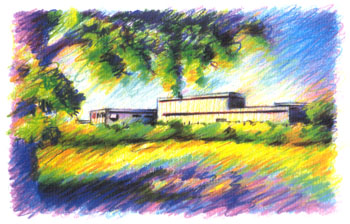 |
Adjacent to I/N Tek, and under the roof of the same huge facility is I/N Kote, a 50/50 joint venture between Inland and Nippon Steel. I/N Kote is comprised of a 400,000 ton capacity electro galvanizing line (EGL) and a 500,000 ton hot dip continuous galvanizing line (CGL), which supply zinc and zinc-nickel coated steel to the automobile industry. Initially, I/N Kote's principal customers were Japanese auto manufacturing transplants located in the United States, but today approximately 50 percent of the firm's production is sold to American automakers. The creation of this joint venture was publicly announced in September 1989. The EGL officially started production in September 1989. The EGL officially started production in September 1991, while the CGL began commercial operations two months later in November 1991. Since opening, I/N Kote has made in excess of 1.75 million tons of galvanized steel on the EGL and 1.65 million tons on the CGL.
A Join Venture Built on Participation and Labor Management Partnership
During 1983 and 1984 the leaders of Inland Steel Company, after experiencing many years of increasing costs, declining profits, and shrinking market share, began to seriously discuss the need to develop a new strategy. Revitalization of the firm's market position and profits were clearly first contingent upon major capital investments in new technology. Because the world's most advanced continuous cold rolling technology had been developed by the Nippon Steel Company, the leaders of Inland Steel initially planned to purchase outright an entire new plant and equipment, but the cost proved to be far too expensive given Inland's precarious financial situation at the time. Consequently, negotiations which had started between 1983 and 1984, began to shift in 1984 from bargaining to purchase toward talks of establishing a new joint venture.
"Conducting labor management relations in the new framework has required enormous risk and trust on the part of both parties, but the result has been an agreement and a labor management relationship that can be rapidly modified to adapt to any new environmental condition."
Because of Inland Steel's stronger motivation to create this new enterprise, and therefore its willingness to assume greater risk, the final agreement involved a 60-40 split, with Inland Steel holding controlling interest. However, as the two parties neared their final agreement on I/N Tek, Nippon Steel began to express a deepening interest in strengthening its position as the favored supplier of galvanized sheet metal to U.S.-based Japanese transplants. Therefore, Nippon Steel initiated discussions on the possibility of broadening the new alliance to include a galvanized operation, I/N Kote, based on a 50/50 partnership.
USWA: A Union Partner From the outset, both joint ventures have involved a highly participatory and collaborative effort between Inland Steel, Nippon Steel, and the United Steelworkers of America (USWA). Indeed, I/N Tek and I/N Kote provide a significant case of participatory designs and implementation.
Not long after official announcement of the formation of I/N Tek in 1987, an initial contract was negotiate between the USWA and the new company. Moreover, it was also decided to initially create only a "bare bones" agreement, which very broadly and generally articulated in writing the basic principles and philosophy of team-based design, join consultation, compensation, and employee rights. Indeed, at this point even the idea of gain sharing amounted to only a brief statement that the parties agreed that in the future they would develop a performance-based bonus program.
The contract was also to become a "living document," which would be continuously open to facilitate development of new contract language to deal with issues and needs as they arose. Consequently, between 1990 and 1993, while the operations and organization were still in their formative stages, some 20 different memorandums of agreement were added to the contract, compared to the only five or six from 1993 through 1995. Although the contract is kept continuously open for negotiated adjustments, this is not the case for the economic aspects of the agreement, which are renegotiated every three years.
Conducting labor-management relations in this new frame work has required enormous risk and trust on the part of both parties, but the result has been an agreement and a labor-management relationship that can be rapidly modified to adapt to solved on "real-time" basis as opposed to letting matters wait, conflicts fester, and opportunities be missed until the next scheduled negotiations. At every step of the process, management, union officials, and employees have worked together as partners in designing and implementing the new organizational structures, work systems, production processes, and reward systems. From the start, both company and union leaders have been committed to creating these new operations based upon sociotechnical design principles, with the ultimate goal of producing a superior quality.
Outcomes
The results from this arrangement have been greater efficiency, dramatically increased equipment utilization, and high levels of job satisfaction and commitment among workers. For example, what previously would have involved five different production steps and fully a 12-day period to produce at more traditional steel mill is now one continuous cold rolling process that takes under one hour to complete at I/N Tek. Since early 1992 I/N Tek has succeeded in achieving an average rate of continuous systems operation equal to 90 to 100 percent of scheduled production hours. Management levels have been significantly flattened, and 70 percent of the time both operations run without any management personnel on site.
Workers have also indicated considerable satisfaction with the new design. In response to a survey conducted in 1994, they unanimously answered that they were very committed to the new work system design, they preferred working in teams over individually based job assignments, and that their jobs were literally the best jobs they had ever had. Both company and union leaders are also deeply committed to the philosophy of continuous improvement.
Employee Involvement and Teamwork: Design Process and Structure
Employee involvement began early in the process, well before the plant had been built and production started; for the management group and the USWA agreed that these workers would work directly with the management team and nonunion staff in designing the new organization. Before the new management team had already invested a great deal of time and effort into learning about sociotechnical systems design principles and continuous improvement processes.
Management representatives from both Inland and Nippon Steel attended workshops on sociotechnical systems design as early as 1986. During that same year 13 section managers from Inland Steel traveled to Japan to see the new technology in operation and to learn about kaizen, or continuous improvement, at Nippon Steel's cold rolling operations in Japan. Five managers stayed on site in Japan for a full five weeks and eight stayed from two weeks.
The learning process continued throughout 1987, and during 1988 the new management team for I/N Tek invested more that 1,000 hours of working together on the basic design of the new organization at the strategic, administrative, and operational levels, with the guidance and assistance of external organizational design consultants. A number of site visits were also made to model high-performance systems, including Cummins Engine Company's Jamestown, New York, plant and the operations of General Motor's Saturn Corporation.
Designing the Organization Central to the new organization's design was the development of a management system, production process, and approach to equipment maintenance that would enable the new enterprise to reach for higher levels of continuous, uninterrupted production. The approach for accomplishing this objective began in 1986 when the group that had gone to Japan conceived of equipment control strategy for system maintenance and what they termed the Inspection Method of Maintenance.
"Workers unanimously said that they were very committed to the new work system design, that they preferred working in teams over individually based job assignments, and that their jobs were the best they ever had."
In order to ensure profitability from the new highly capital-intensive continuous process technology, the new production system had to operate at no less than a working ratio of 90 percent or higher. It was also necessary to minimize the amount of time taken to maintain equipment by shutting it down, because shutting down any one part of the process would also halt the entire system. To achieve these objectives, it was determined that both plat operations and maintenance team members would have to process a high level of knowledge and understanding of the new production processes and equipment, have a strong sense of ownership of the new technology, and have sufficient responsibility an decision-making powers to carry on all the necessary duties involved with monitoring and caring for the production technology. In short, operators and maintenance technicians alike would maintain constant vigilance over the production system, using highly developed skill and sophisticated instrumentation tools to ascertain on a continuous basis whether equipment was running at peak performance or under stress.
Maintenance craft employees-equipment control personnel under the new strategy-would also take responsibility for the continuous improvement of maintenance processes. They would be expected to improve equipment monitoring and testing tools and techniques, take responsibility for planning and scheduling shutdowns, and check, repair, and replace equipment and parts before actual disruption to the product on process could occur.
Recruiting a Workforce During the summer of 1988 through January and February of 1989, the realization of this plan began to take place with the recruitment and selection of the initial I/N Tek workforce. Consistent with the new philosophy of maintenance and operations, the first positions that were recruited were the equipment control personnel followed by operations specialists. Because of the high-level technical skills required for these jobs, recruiting took place at Inland Steel's Indiana Harbor Works, with the first option given to the employees already working in the cold rolling production. This was a collaborative effort on the part of both management and the union, but the process was very different from the traditional job bidding procedure.
Interested applicants were told a great deal about the new company and its very different work philosophy and system. Those who were still interested were required to fill out applications, including a resume and a letter the explained why they wanted to be part of the new venture. Then the evaluation process began: a prescreening interview; a rigorous testing procedure, including aptitude tests, a day long exercise, and work simulations; and three or four targeted interviews.
From The final pool of applicants for initial positions on the operating and equipment control teams, only 117 out of more than 1,000 applicants were actually hired. Initially, 30 equipment control specialists were hired, and they began work on planning the new system in October 1988. This group received comprehensive training in sociotechnical design principles and analysis in workshops on "what do teams do" and "training the trainer," from consultants who acted and facilitators and technical consultants during the design process.
"Operators and maintenance technicians would maintain vigilance over the production system, using highly developed skills and sophisticated instrumentation to ascertain whether equipment was running at peak performance or under stress"
In January and February 1989 the rest of the equipment control group were hired, as well as operations personnel. When these people started work, they also received training and helped in the designing process. In total, 54 of the initial I/N Tek team were recruited for operating positions and 63 for equipment control positions.
Consistent with the strategy of achieving maximum equipment utilization, 24 of the original 54 individuals hired to become operators were also certified working mechanics. Subsequently, during spring and summer 1989, all 117 craft employees were sent to Japan to learn the new technology firsthand by working side-by-side with their Japanese counterparts at Nippon Steel's Hirohata Works for periods ranging from six to ten weeks.
Further Design Efforts
The design team met every week on a regular basis from October 1988 through March 1990. Unfortunately, during this period the team was not able to fully complete its work on designing the social side of the new organization, including a detailed delineation of decision-making roles and lines of communication. Once the new equipment had arrived in June 1989, the pressures to get the new system up, running, and generating income took precedence, and therefore, concern with dealing with the social system diminished, as one process mechanic, formerly a member of the original design team, explains:
The equipment showed up and we told ourselves that we needed to get it up and running and making a profit as soon as possible. We thought we could concentrate on the social side later on. At that time we felt a lot of pressure to start making some money right away. Inland was laying people off and we were working 60 to 80 hours every week.
Thus, the initial team structure and organizational design had not been worked through completely when I/N Tek first started production. Not surprisingly, the first efforts at functioning on a team basis were therefore somewhat difficult. Another member of the original design team also explained during an interview that this was especially true for the teams originally organized to perform equipment control, then called the State Change Technical Teams.
Because they were too large, there was no clear leader or leadership, and no direction from management on how to set priorities. Also the present was changing too much, with everything in flux at that time. It wasn't a priority to be a team at that time. It was a priority to keep running!
It was also the case that we had intentionally seeded this place with people who were very much technically oriented business types, so naturally the social side of things was not so much a priority to them.
Thus, by late 1990 it had become clear that further design work was necessary if a smoothly running and efficient system of self-management was to be realized at this point. Beginning in early 1991, management, union leaders, and the entire workforce participated in a system-wide redesign process, described on p. 52.
The organizational structures and management system that evolved through both the initial design process and the redesign process described above have helped to bring human and technical resources together in a powerful and dynamic combination. High levels of employee involvement, self-direction, and autonomy, implemented through a system based upon self-managed work teams and joint consultation, are the foundation of this high-performance system. The basic structure, which is continuously modified and updated as social and technical growth takes place, now looks like this:
Customer Product Teams take responsibility for all phases of production from the beginning to the end of the production process.
The composition, structure, and powers of each CPT are based on the design principle of instilling a strong sense of ownership over the product and the entire production process during each of the four shifts, beginning with Receiving and ending with Shipment.
CPTs are responsible for managing and controlling all aspects of the production process and ensuring that the product meets customer's specifications precisely.
CPT members perform a wide range of managerial activities and functions that in the past were traditionally the responsibility of first-line supervision.
The managerial and administrative duties of CPTs include ensuring that operations are performed in budget, controlling inventories, controlling and eliminating scrap, keeping records, scheduling production, continuously checking and maintaining product quality, scheduling work and vacations, making job assignments within the team, planning and coordinating the training of team members, coaching and counseling fellow team members and interfacing with customers and external resources such as vendors and suppliers.
Boundary Groups are sub teams of the larger CPT. These groups were established in part because the size of the CPTs made them too large and unwieldy (in the case of I/N Tek, 30 people), to serve as teams that can work and meet together daily on a face-to-face basis to share information, solve problems, make decisions, and rotate job duties. Boundary groups were also created to enhance the effectiveness of team-based management and control of the different, distinct "state changes" involved in the total production process. Each boundary team is responsible for all aspects of the production process involved in accomplishing a specific state change.
One representative from each boundary group also serves as a representative and member in the regular meetings of the CPT. By themselves, boundary groups also meet daily prior to their shift for at least a 30 minute period to coordinate with the outgoing shift, replan, and make adjustments for their own shift. Boundary groups are responsible for their own daily self-direction, including dividing up the assigning tasks for the day, week, and month. These groups also hold a longer meeting once each month for at least two hours to plan the month's key events and activities.
Equipment Control Teams were established to perform the maintenance process following the strategy of equipment control through inspection.
Process mechanic are organized into Core Mechanical Teams, and process electricians and electrical inspectors are members of Core Electrical Teas.
These two teams, as the term "core" indicates, are responsible for all aspects of monitoring, testing, maintaining, repairing, rebuilding, and replacing the equipment directly involved in the production process.
The third type of equipment control group, Auxiliary Teams, are responsible for ensuring that tall buildings and machinery involved in support of the core technical process, but not directly part of it, are kept in top working condition.
The Equipment Control Teams have a wide range of powers and responsibilities, including developing boundary budgets; planning and conducting all inspection procedures, data collection, and analysis on equipment and system performance; conducting failure analysis; developing and maintaining spare parts inventory; planning repairs and shutdowns; performing repairs; and interfacing with vendors and contractors, including planning and scheduling contractor services during shutdowns.
In order to maintain and increase team cohesiveness and effectiveness, as well as enhance the overall quality of decision making, all teams were trained in consensus decision-making skills. The emphasis was on making decisions that all members can live with and support. However, the actual implementation of this process was far more complicated than the espoused ideal because of the substantial change which both managers and workers had to make in moving from the old adversarial relationship and autocratic management system to the new participatory environment. As one manager explained during an interview:
When we started these meetings, they were almost like wild animal meetings, with everybody yelling and screaming and talking at the same time. But all of these guys have been trough facilitator training, and so now the meetings are very productive, because they know how to manage the meetings and handle differences of opinion.
Finally, the principle of commonality was adopted so that the spirit of teamwork would not be undermined by creeping social differences.
- Everyone wears the same uniform
- No preferential parking except for the company nurse
- One common cafeteria shared by all
- A common fitness room and locker room (separated by gender only)
- Family visits involving the families of all members
- A family wellness program for all members
- No time clocks for all members on salary
Labor-Management Partnership
Creating and sustaining a true labor-management partnership was integral to the success of I/N Tek and I/N Kote from the inception of these new enterprises.
The initial agreement that was negotiated between the company and the USWA began this collaborative process, and Tom Jones, international representative for USWA District 7, worked with management in the design process even before the first union members had been recruited. The cooperative ideals underlying these partnerships are well understood by all employees.
They begin with a clear and specific elaboration of the shared community of interests between the company and the union articulated in Section II of the collective bargaining agreement:
The guiding principle is that the enterprise (companies), and the union and employees all share a community of Interest and a common goal to be achieved through team work and joint participation...Implementation of this principle will result in continuing improvement and quality and…efficiency and...will produce employment which is both more satisfying and secure.
The contract also clearly outlines the responsibilities, commitments, and expectations of both parties in fostering the partnership. The Company's desire is to produce the finest cold rolled and coated steel products in the world.
In order to do so, it is necessary to insure a cooperative partnership among all concerned in a framework built upon mutual trust, respect, and a sense of dignity.
The union is guided by three concerns:
- First, that the technology requires a new approach to the allocation of work tasks.
- Second, that the Agreement creates an opportunity for full employee participation in decision making, and in a new form of industrial self-governance.
- Third, and most important; the Agreement enhances long-term employment security.
Implementation of the partnership is achieved through a wide ranging system of joint consultative committees such as those created at I/N Tek (fig. 1, p. 54).
Through this committee structure, and a similar but not identical system at I/N Kote, is has become possible for union-management cooperation and employee participation to be realized in an ongoing process of continuous improvement, cutting across all three levels of organizational performance strategy, tactics, and execution.
The cultural atmosphere at both I/N Tek and I/N Kote also strongly emphasizes cooperation and collaboration. Information flows freely and openly between the two parties.
Both operations are also open to international representatives to visit and communicate with local officials and members at any time during the day or night.
At the strategic level the Joint Advisory Team, the Leadership Committee, and the Strategic Business Team define company goals, policies, and the allocation of resources.
At the tactical level are a number of committees composed of employee and management members who work to develop the plans, programs, and projects that realize strategic objectives.
Joint labor-management groups at this level also perform the critical roles of administering, coordinating, and providing support for company-wide programs and projects.
Likewise, at the tactical level are the Management Resource and the union Team Representative, which in the I/N Tek and the I/N Kote cultures are the counterparts to the first-line supervisor and the union grievance committee person or shop steward.
Last, at the level of execution are the actual work teams.
To describe the roles of all these groups is beyond the scope of this case study. A few of the key and perhaps most unique groups, however, are briefly described below:
Management Committee
For I/N Tek and I/N Kote this group is the equivalent of the board of directors. These are the highest level management policy-setting groups for the two enterprises. These groups meet twice each year - once in June and once in December.
In the case of I/N Tek, three members represent the interests of Inland Steel and two members represent Nippon Steel.
I/N Kote's management committee has balanced representation from the two firms of three representatives each.
Joint Advisory Committee
This is the primary union-management consultative body at I/N Tek and I/N Kote. There are 12 members on the JAC, including al the top leaders of both the union and management.
On the union side this includes the international representative for USWA District 7, the president and vice president of Local 9231, the dispute resolution chair, and one member-at-large elected from each of the two companies.
On the management side the members include the company president, the vice presidents of operations for I/N Tek and I/N Kote (these two vice presidents are Japanese executives), the manager of human resources (human resources and labor relations are one function), and the operations/maintenance managers from each of the two companies. Under regular conditions this group gets together once a month for an all day meeting that lasts from 9 A.M. until 5 P.M. When critical problems are being confronted and solved, they meet much more frequently.
Leadership Team
This group meets twice each month to share information and discuss important issues, needs, and plans related to production, people, and quality.
Strategic and policy decisions made by the Management Committee or the JAC are also shared and discussed at these meetings as well as important communications and information sharing between I/N Tek, and I/N Kote managers and union representatives.
This is a very large group, with some 30 persons regularly attending, and therefore, this is not a decision-making group. However, the Leadership Team does create ad hoc problem-solving committees to study and develop solutions to nonpolicy problems.
All members of management belong to this group except for first-line management resources.
All of the union representatives who are members of the JAC are also members of this committee.
Strategic Business Team
All members of management belong to this body, including the first-line management resources. All top union officers also belong to the strategic business team except for the dispute resolution chairperson. The committee member-at-large on the JAC is also a member of this group.
The strategic business team is responsible for regularly sharing information, planning, and solving problems related to the overall business and manufacturing strategies.
Resources and Team Representatives
At the team level the company and union provide leaders who are supposed to work together closely in maximizing both human and technological potential.
The resource is the I/N Tek and I/N Kote counterpart to the first-line supervisor, and the team representative is the counterpart to the grievance committee person. However, the role involves significantly more than grievance handling because, again, the resource is only on site 30 percent of the time or, for example, strictly during the day shift.
Together, these two representatives are responsible for ensuring that all resources are available to enable the team to effectively engage in self-planning and self-direction and to achieve high performance on the line.
Team representatives and resources also serve as a linking pin between management and union leadership and the teams, and therefore, spend a substantial amount of time facilitating both communications flow and the decision-making process.
The team representative also plays a unique and critical role when teams need to counsel employees and take disciplinary actions. Instead of playing the traditional adversarial role, the team representative ensures that actions taken are based on good information and helps the team to work effectively with the team member who is the focus of concern.
Resources do have the power to take disciplinary action on their own, but thus far no such incident has arisen.
Integration of Technology and Social Systems
The entire organizational and management system design of I/N Tek and I/N Kote has been based on the concept of combining social and technical systems in an optimally integrated whole. However, as has been noted, this is a constant and ongoing process.
Currently, both companies are going through a system-wide effort to learn and have begun to apply Total Quality Management principles and methods.
On a more daily basis, the boundary groups play a particularly significant role in constantly realigning and deploying human resources in and effort to continuously improve and increase the efficiency of state change processes. They are continuously involved in an effort to monitor technological processes and try to come up with new strategies and methods for improving the technology and its use.
At the tactical level of action, the Quality councils and its associate committees are constantly involved in the process of finding solutions to significant needs and problems and also planning and scheduling training related to continuous improvement and TQM.
Communications and Information Sharing
A great deal of both lateral and vertical communication flow is facilitated on a regular and ongoing basis, especially by the resources and team representatives an I/N Tek and I/N Kote. All members and teams also have their own e-mail addresses, and the e-mail system is used actively to facilitate the communication between teams, shifts, functions, and individuals as well as between top management and the entire membership of both organizations.
In addition to the sheer quantity of information that is shared, and the variety of channels that have been created to facilitate the flow of information, it is important to remember that underlying the success of this system is a degree of trust, especially between management and the union and its members. As Tom Jones explained:
John Nielsen [head of human resources and the company's chief negotiator] and I operate on a couple of premises...We do things, we don't lie to each other and we try to minimize surprise. If something is coming down the pike that I know about, I try to say, "You should be aware that there are issues here that are rising," so he isn't surprised.
Therefore, I'm looking after him; he knows that I'm not going to stab him in the back; and I'm not out there taking unfair advantage.
I'm a very direct person.
On the other hand, I develop confidence that he will share with me those things that he can when he knows them and in a timely manner. We don't lie to each other and we don't have surprises.
Achievement Performance Measurement
Establishing clear and meaningful performance goals have been integral to the success of I/N Tek and I/N Kote from their inception. However, providing the data to those individuals and groups responsible for actually executing the production process and getting a superior quality product to the customer was not initially well linked to the design process.
The consulting group commissioned to develop the performance measurement and information systems had initially based its program on bringing information from the teams to top management instead of from management to the teams - the people doing the core work of the plant.
The system it devised would enable plant-level managers to control the process instead of giving core workers the information they needed to participate in the process.
With a fresh understanding of the participatory nature of the plant and its sociotechnical principles, the group was able to devise a more appropriate system.
From this point on the organizational design and the design of the performance measurement and the information system began to be directly correlated, and today, extensive data on daily, weekly, and monthly performance on a wide array of variables is provided to CPTs, boundary groups, and equipment control teams.
When it comes to the most critical variables, such as the system working ratio, tons produced per month, cumulative production, and product quality information, performance data are reproduced and displayed on large, easy-to-read, multi-colored charts and tables, which are displayed in team meeting areas.
Quality and Customer Focus
A quality- and customer-oriented focus is fundamental to organization design and the system of self-management at I/N Tek and I/N Kote. Team members are collectively responsible for both product quality and customer satisfaction. Their performance includes not only making a product precisely to customer specifications and expectations, but also delivering it to customers exactly when they want it and in a way that they want it delivered.
More recently, both I/N Tek and I/N Kote have adopted TQM systems. Statistical quality control data are used extensively for the purpose of monitoring quality performance against goals, identifying quality problems and needs, and solving quality problems.
Training and Continuous Learning
The development, operation, and continuous improvement of complex systems depend upon a workforce that possesses a very high level of technical, social, and managerial skills. Thus, it was imperative for I/N Tek and I/N Kote to invest heavily in training and continuous learning.
Evidence of the heavy investment of both money and time in training and education is readily apparent. For example: A total investment of over $100,000 per worker was made in training and preparing the initial equipment control and operating technicians for their roles in the new plants.
Eighty percent of I/N Tek's initial workforce was sent to Japan for a period of from two to ten weeks to learn through on-the-job experience and direct observation about the new production technology and their new work roles. Every year all members attend a minimum of from two to five weeks of additional training related to both skills upgrading and refresher courses.
Redefinition of Staff Support and the Managerial Role
Both management and staff support personnel act primarily as resources to CPTs, boundary groups, and equipment control teams. Their work ensures that the team members involved directly operating and supporting core technical processes and interfacing with customer needs and demands have all the resources, information, and training necessary to perform their work effectively.
This is particularly true of the first-line team of management resources who work directly with the teams that serve as linking pins to other teams and staff departments, as well as in a boundary-spanning role with external groups.
Resources have also been trained to serve as coaches and team facilitators rather than acting as the ultimate front-line decision makers and authority figures.
The importance of these new roles cannot be overestimated because management personnel, including resources, are only on site 30 percent of the time each day. If resources were unable or ineffective in helping teams to function properly and effectively as self-managed groups, production would soon grind to a halt.
Another important change in managerial roles is that of human resource management.
The top human resource manager, John Nielsen, and his HR team now act as facilitators of harmonious relations and open communications between the workforce, the union, and management as opposed to the traditional role of advocates for management and shareholder interests. An important part of this new function has been the Project Office, which is part of the HR department but is staffed by both union and management personnel.
The Project Office was established in 1991 to develop a comprehensive skills matrix and a systematic certification process for operations, equipment control, and material handling positions.
Since completing work on the skills matrix and certification process, the Project Office and its members have played a key role as internal trainers and change agents who support and push both companies toward more fully realizing their social and technical goals and objectives.
Union leaders, and particularly international representatives, now also play a facilitative role in reaching cooperative solutions to their members' needs and those of management and the companies. Thus, the role of the district director in labor-management negotiations has become one of helping local union officers and management clearly articulate their concerns and interests, and then facilitating a problem-solving approach to the final negotiated settlement.
Rewards
Compensation Systems
The compensation systems developed for I/N Tek and I/N Kote are directly correlated with both the short-term and the long-term organizational performance. However, arriving at such a system has been the result of a process of evolution as opposed to a preplanned and negotiated blueprint.
Over the years I/N Tek and I/N Kote have developed a compensation system that encourages hard work and creative effort, and motivates employees to increase their level of knowledge and skill through continuous training.
The compensation system also creates a strong spirit of community and shared interests. The key components of this system are as follows:
All members are on salary with no differentiation based on either skill or hierarchical level.
There are no time clocks, so hours are credited, using a self-report system.
Depending on job classification and the skill level at which an individual has been certified in that classification, base compensation can range from $28,000 to $42,000 in salary per year.
Basic compensation is founded upon payment for skill and knowledge.
There are five basic job classifications with different degrees of competency within each job classification category. Base compensation is determined by what level of skill and knowledge within a given category a team member has attained.
The highest level of skill and knowledge attainable in all job categories, except material handling, all pay the same top rate. To obtain increases in pay each member must advance to the next highest level of competency within his or her own technical field.
Skill areas in which members must certify in order to qualify for the highest competency levels cover several categories, including job-specific technical skills, business skills, TQM, safety, and social skills.
Variable compensation is based on both gain-sharing and a variable incentive plan, which together are called the Achievement Sharing Award.
Bonus awards for both components are paid regularly and profit sharing were not adopted until after binding arbitration had determined what program criteria would be adopted in 1990.
Variable Incentive Plan bonus payments are based upon business outcomes and overall profitability, and all members receive the same dollar amount in bonuses regardless of position or title. Average quarterly bonus income has been approximately $4,000 for both companies.
Recognition
There are no formal system-wide programs at I/N Tek and I/N Kote for recognizing either contributions of individuals or groups.
Inland Steel Industries, however, has several recognition programs, with the most prestigious award being the Chairman's Award, which is presented on an annual basis.
Over the years since I/N Tek and I/N Kote first commenced operations, several teams have been recognized by receiving the Inland Steel Industries Chairman's Award.
Quality of Working Life
As much of the foregoing discussion has already indicated, I/N Tek and I/N Kote were originally designed, and have since evolved, to be not only high-performance organizations but also organizations that provide a high quality of working life for their members.
Employees have responded to organizational surveys by stating that their jobs are literally the best jobs they ever had. They have also indicated that they highly value the opportunities that they have to learn from, and work with, highly competent and qualified peers.
On the other hand, they have also said that their jobs can at times be extremely demanding and even stressful. Some members have said that although the income they receive from extensive overtime work is extremely beneficial, it also takes its toll and they routinely find themselves working more overtime hours than they would like.
Beyond modifying and adapting work practices and management systems, I/N Tek and I/N Kote's have also attempted to improve both the health and the general quality of life for their members through sponsoring wellness programs and also providing exercise and fitness facilities on site for use by everyone.
Employment Security
Over many years both researchers and practitioners have learned that the essential conditions for achieving and sustaining high-performance work systems are providing all employees with both employment and income security.
High-performance work systems demand from team members an unusual level of loyalty and commitment to their jobs, to their fellow work team members, and to the enterprise as a whole. Members should be willing to devote their utmost effort and creative energies to continuously improving operational performance, responding to change with flexibility and agility, and meeting and even exceeding customer expectations.
Rational employees will not invest this much in their work lives if they must constantly or even periodically worry about the security of either their jobs or their incomes.
Consequently, I/N Tek and I/N Kote provide strong contractual commitments to al employees in regard to these two very fundamental issues. However, there is some degree of differentiation between the most skilled equipment control and operating positions and the material-handling group.
These provisions form Section VII of the Collective Bargaining Agreement are cited below.
The parties are committed to managing the enterprise in a manner, which will maximize the opportunity for continuous full-time employment. Consistent with this philosophy, employees must be given reasonable guarantees of a stable livelihood.
Accordingly, no USWA team member established in the operating Attendant or Equipment control Skill Based Classifications (approximately 75 percent of the workforce) shall be laid off but for catastrophic events of such magnitudes as to impair the economic viability of the facilities.