Automation And Work Design In The United States
Automation and Work Design - 1984 - By J. Fadem, P. Gustavson and J.C. Taylor
Edited by Federico Butera and Joseph E. Thurman
Ch. XVI Automation and Work Design in the United States
(By J. Fadem, with a case study on socio-technical design and new forms of work organization: integrated circuit fabrication, by P. Gustavson and J.C. Taylor)
2.1 Introduction
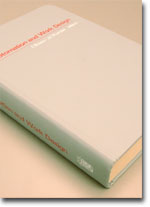 |
This chapter was featured in Automation and Work Design. |
The introduction of the microprocessor has dramatically lowered the cost and expanded such applications of industrial automation as cybernetics, robotics, NC machines and CAD-CAM. However, apart from the automatic control of production processes, automation has eliminated the need for certain controls, because of radical change in product technology.
The continues development of the microprocessor since 1970 has relied in turn on developments in photolithography which have permitted a remarkable miniaturization (called large-scale integration - LSI) of circuits; and of achievements in physics and chemistry, especially the metal-oxide-silicon (MOS) process of fabricating transistor-based semiconductor circuits. Such technical breakthroughs as these suddenly moved computer electronics from a labor-intensive to a capital-intensive industry. A decade ago, workers with soldering irons meticulously hand assembled and wired separate electronics components such as transistors, condensers and resistors on to metal frames; today, a few workers monitor sophisticated equipment to fabricate computer chips in batches of up to 4,000 LSI circuits at a time. No soldering of separate components is done because with MOS and similar technologies none is required; such new semiconductor technologies have permanently altered the fabrication of computers and other similar integrated circuit devices. It is as if the new fabrication facilities were automated on the conventional sense (for example, many workers have been displaced or made redundant) but it is the product technology itself that has changed the production process, rather than merely the computer control of the process. Indeed, the MOS process involves the use of computers for automatic control, but the basic worker activities of handling the silicon wafers often requires human intervention and override rather than mere monitoring of machine activities.
Automation and worker displacement are connected, but the major automation question in the United States during the seventies has been not whether, but how, the jobs that remain after automation can be changed for technical effectiveness and improved in terms of QWL. The American dilemma has been how to reconcile the industrial era assumption s of technological determinism with the post-industrial requirements for coping with unpredictable, stochastic events. Technological determinism leads to the conclusion that technology is the most important element and that jobs, work and organization must be subordinated to support it; it assumes that there is "one best way", and that way is called for by the technology. Although the dilemma is not yet resolved, North American experience is accumulation to show that new forms of work organization, designed to address social and psychological requirements as well as technical ones, are better able to provide for the flexibility of organizational response, which currently characterizes a successful system. American managers are beginning to realize that work teams or groups are more appropriate units or organizational learning and system interdependence than re individual workers are supervisors. Attempts to trace the developments of the American industrial revolution, farther by F.W. Taylor, backwards from 1920 to the factory system of the British industrial revolution, and forward to the United Stated human relations and job enrichment movements of the fifties and sixties, lead to the conclusion that the focus on the individual jobs and workers is responsible for the success of the American industrial system from 1910 to 1960, and also responsible for the decline in productivity since then. 98
The United States electronic industry has grown up literally since the period of shift in American fortunes. It is an industry, which was developed both in large laboratories at IBM and AT&T, and in backyard workshops in Cambridge, Massachusetts and Palo Alto, California. Because so much of the industry started on a small scale and grew so quickly, the amount of concern for organization design at all has been minor in relation to desire for technological innovation, and the pursuit of private fortunes. Thus the organizations we see in current United States electronics firma re inadvertent copies of the Tayloristic model, which contributed, to industrial success between 1910 and 1960, and to decline between 1960 and 1980. Although the capital investment in microelectronics technology (e.g. LSI and MOS) has provided a marked improvement over the earlier products in cost and availability, the American microprocessor industry has not been able to compete favorably with the Japanese when both are using similar production processes for similar products. American managers in microelectronics have become attentive to Japanese production and managerial methods, but have done little except emulate the employee suggestion plan embodied in quality control circles.
In North America, socio-technical systems as an organizational design approach provided a marked improvement in organization al effectiveness and QWL during the seventies. Social -technical systems design is a conscious effort to examine and evaluate the structural aspects of organizations (including division of labor, job design, work group definition and performance measures), and to guide and justify subsequent changes in structure. Socio-technical designs often o=involve teams of workers, and the nature of these groups (whether face to face, group size, time boundaries, supervisory roles, multiple skills and specialties) are determined by the objectives and philosophy of the system, employee capabilities, prior labor agreements and technical requirements. Over periods of up to 20 years, socio-technical systems designs have proved durable in their continuance and ability to adapt. The socio-technical systems concept has its roots in Europe rather than Japan, and it represents in the United Stated a way to begin to substitute a strong social organization for the individual worker/supervisor model of the earlier American industrial designs.
The present case study illustrates the use and effects if socio-technical design methods in microprocessor fabrication. It represents an excursion into organizational design, anew area for the industry, and it shows how effective both in speed of application and in permanence of effects socio-technical designs can be. The semi-conductor industry is not widely trade unionized; no experience thus exists which deals with union-management co-operation in the industry. The identifiable audience for immediate change is therefore management, but it is hoped, in addition, that the material and its conclusions will also encourage actions taken directly by workers.
2.2 Lessons from Japanese competition
The Japanese excellence in microelectronics manufacturing is a powerful stimulus for the American electronics industry to consider new ways of working. This is demonstrated in the new Nampa, Idaho, semiconductor plant Zilog, Inc., a subsidiary of Exxon Enterprises and the producer of the Z-80, the industry standard for 8-bit microprocessors.
If asked whether Japanese methods of production had been the model for organization, Zilog management would rely that their design techniques are largely based on those of the United States and Europe. It is maintained here, as elsewhere, that United States organizations cannot simply uproot the Japanese management style and transplant it to American soil. However, there are several ways in which the traditional American management approach can benefit from the Japanese.
In America microelectronics, as in other industries, workers are regarded as liabilities. The result has been an increasing disconnection between American employees and their products. Workers are assigned to pieces of equipment where they perform a repetitive, narrowly focused job such as pushing a button or looking through a microscope. They are taught to make decision whose impact they do not understand, based on information they do not understand. The button pushing becomes an endless series of meaningless tasks. In Japan, occasional mistakes, particularly those made by lower-level employees, are considered part of the learning process. If employees are not successful in a particular job, they are transferred to amore suitable position in the company. In the United States, and employee mistake more often results in punishment; and employee who makes the mistake twice is often fired. The rational is that if that kind of behavior is tolerated, everybody will be doing it. Therefore and example is made of the worker concerned.
Another characteristic of American industry is that organizational structure is shaped like a pyramid, with all the decision-making power at the top. This has remained true especially in the semi-conductor industry, with its rapidly changing technology, highly complex products, and relatively few people with broad knowledge of those products. At the lowest levels of the organization - the levels where the products are actually built - there is almost no information available beyond a specific directive to push a button on a machine. The product itself has no meaningful context, and so the job as no meaning. Average turnover in the American semiconductor industry has ranged from 50 % to 100% annually between 1978 and 1981, during a period when the national average has average half that rate.
2.3 The project
The company was preparing to open a new microprocessor chip manufacturing plant in Nampa, Idaho, scheduled for 1979. All of those who were involved in the project were managers, and had taken part in previous plant openings. They has all experiences the high level of problems involved in start-ups, with the lengthy period needed to bring operators and process engineers up to "speed", and a considerable amount of early personnel turnover. They therefore wanted to improve on this performance. In addition, they set themselves some "unreasonable" goals. Table 91 presents these start-up expectations, compared with industry standards and actual achievements. To meet production needs, management had to get the new plant running in about two-thirds of the normal 18-month period needed to start up such an operation. At the same time, they had to achieve higher-than-normal yields of product quality. Since they realized that these goals were very ambitious and they might not be able to meet them fully, they began looking for a new approach to organizational design.
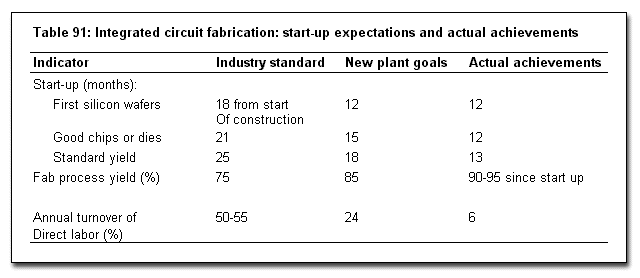 |
2.3.1 Background
In the late 1978, the company hired an experienced plant manager, who had already established an assembly plant in Indonesia, for the express purpose of starting and running the new plant. In approaching the design of a new plant organization the new plant manager observed that the role of management in the semiconductor industry is traditionally based on the idea that manufacturing workers are a liability: "You tell them what to do and how to do it, but there in no prerequisite for explaining why". IN the more traditional plants in the industry, people are place at equipment basses. They are taught how to push the buttons, but they arte not taught what they are doing from a product output standpoint.
In the spring of 1979, after working for several months at Zilog's factory in Cupertino, California, the plant manager began searching for a successful model in start-up ventures. Not only was he looking for a method of structuring the plant to produce a good-quality product with control of costs, but there was pressure to have the plant running in less than the normal one-and-a-half-year period.
In 1979, semiconductor firms in "Silicon Valley" (as the stretch of California between Palo Alto and San Jose is now called) were beginning to expand outside the area. Most had an establishment wide base of operation in the "Valley" to support new ventures in other states. At the time, the company's semiconductor manufacturing group in Cupertino was small, and it was management's decision to leave it small, expanding manufacturing outside of California. For a small company with an adequate but by no means ample technical and managerial staff, it was a risky venture. The new plant represented an investment of several millions of dollars 700 miles away. The site selection had been made 1977. The area offered a stable labor base and water resource to support a reasonably sized semiconductor plant, while the specific location was in close proximity to a major airport, had good educational facilities and was a growing center for new companies.
The prevailing assumptions of manufacturing a management in the Cupertino factory were orthodox, ad typical for 1979. Jobs were reduced to their minimum requirements: and specialization, job behavior and compliance were valued more than success or results. A conventional "wafer fab" environment is organized around two distinct technologies: diffusion of elements or dopants, which deal with growing or construction the silicon wafer's surface; and photolithography, which deals with the circuit geometries of that surface. Figure 34 shows the flow of a silicon wafer from raw material to finished circuits ("chips" or "dies") in a conventional plant, and graphically illustrates the 40 or more times a wafer changes hands (and ownership) during the process.
Fragmentation of work at Cupertino was manifest not only for the basic hourly workers (called "fab operators"), but fro all others involved in manufacturing as well, including process engineers, engineering assistants, maintenance workers, inspectors, supervisors and managers. Jobs in the conventional "wafer fab": (manufacturing) facilities vary little throughout the industry. In evidence of this, the job descriptions for the Cupertino plant correspond closely with those of the salary survey service bureau, Radford Benchmark, which are familiar to most manufacturers in Silicon Valley.
The basic fab operator's job description reads as follows: "under general supervision the operator performs, during peak periods, one or two specific fab skills at a certain level". Specific skills might include alignment of photolithographic mass on wafers, or operating a diffusion furnace. Other activities expected of an operator include "… maintaining work leader or supervisor of any repair or maintenance requirements, and completing production records as required". Higher-graded operators are expected to be competent in several skill areas, to be able to fill in for absent co-workers as required, although they are generally limited to performing a single repetitive task throughout a working day. The degree of fab operator task variety, control over work, involvement in decisions, opportunity to learn about the product and about other skill areas (e.g. maintenance, engineering or training) is virtually nil, and the degree of communication between operators and these specialist groups is very low.
Operators report to supervisors whose Benchmark job description includes; "working on problems of limited scope, following standard practices in analyzing situations from which answers can be readily obtained… assigning and checking subordinates' work … and performing the same work as group members". In a typical fab plant at least three additional levels of management preside above the supervisor. Engineering assistants, maintenance technicians and training technicians all have their own pyramids for hierarchical reporting and promotion within the manufacturing plant organization.
This fragmentation and separation of jobs in Cupertino in 1979 was clearly in evidence even to the casual observer. The clear distinctions between the manufacturing specializations listed above were evidence not only by where people worked, but also by the language they employed. At every turn, casual outsiders (if they were allowed into the "clean room" environment of semiconductor manufacturing) would hear a babel of specialized languages. The engineers spoke to one another of electrical evaluation ("eval") "thresholds", and to their assistants of capacitance-voltage ("CV") "plots", but neither could talk to the fab operators or even the fab supervisors about such matters. The fab operators doing photolithography talked about "mask alignment", and those in diffusion spoke of "pushing boats", and "loading elephants". With their conversation so specialized and their jobs so machine-specific, the fab operators had no ability to talk about work related matters with one another if they worked on different equipment. The fab supervisors spoke language of "moving wafers" from station to station, which was comprehensible neither to operators or engineers. Production management spoke of "balancing the line" and cumulative ("cume") fab "yields", and the maintenance workers spoke the electronics and hard ware language of the factory's sophisticated equipment. These different "languages" created a barrier, which extended even into the cafeteria, where fab operators who knew only their own limited machine-based dialect did not sit at the same tables with other operators who spoke in the tongue of their own activities.
What is the most significant about this proliferation of esoteric "languages" is not that these occupational groups in the Cupertino plant could not (and thus would not) speak to one another, but that nobody spoke of the circuit "dies", or "chips", or in any way referred to the product or output of the factory. Everyone was encouraged to do their best at their specialization, but no one was encouraged to consider the microcomputer circuits, which were their product. Such a limited vision, of course, created and perpetuated a provincialism not only within the Cupertino plant, but between it and then new plant starting in Nampa. Because some of the middle managers for Nampa were drawn from this location, some distrust and misunderstanding was carried out of the Cupertino plant, both because of suspicion of the "new ways" at Nampa by some of those with more traditional values, and because of allegations of "Soft-headedness" towards those who transferred by those who remained behind.
2.3.2 The design model
The plant manager's search within the semiconductor industry turned up few models for organizational design that were satisfactory for setting up a new plant in a short span of time. Thus in early 1979 he sought help from the organization development consultant of the parent company. The result was the use of an "open systems model" of socio-technical analysis, which several companies outside the electronics industry had been using for a number of years. The plant manager also became part of a network of plan managers of so-called "innovative plants" who met together several times a year to share work innovation experiences.
Shortly afterwards, the plant manager's subordinate managers (who would later make up the management team in the new factory) attended, with other company managers, including the President, a week-long workshop on organizational open systems design. They also visited other plants applying new forms of work organization and management systems. The plant manager and his management group also met consultants who had worked in plants of a company, which is reported to use open socio-technical systems designs.
The internal organization development manager of the company and an external socio-technical consultant, working together with the plant manager and his team, developed and implemented their own version of an open socio-technical system design for the new plant. The "design team" of managers continues as a planning team today.
In the open systems socio-technical model, the idea is to encourage responsibility at its lowest possible level. It is taken as a premise for such designs that people enjoy making decisions, taking on responsibility and reaching a level of task ownership. In this case ownership meant participating in work-related decision-making, setting goals and implementing them.
The work design process involved three steps. The first step was to formulated the purpose, or "mission" of the plant. Simply stated, the plant mission was to produce high-quality integrated circuits (in other words the individual microprocessor circuits "chips") at a minimum economic and social cost. A key distinction here is that the goal was to produce good circuit chips, not the silicon wafers upon which a number of identical circuits are simultaneously fabricated. The importance of this distinction cannot be over-emphasized. It would force each worker to think in terms of an end product, a result, instead of an isolated process or an interim step. The conventional semiconductor manufacturing facility had two separate processes: wafer fabrication (wafer fab) and wafer sorting. Wafer fabrication refers to the manufacturing process itself, in which as many as 250 separate circuits are constructed on and in the silicon wafer. Wafer sorting, on the other hand, refers to testing the finished circuits on the wafer and identifying the faulty ones. This distinction had no meaning in the new plant. At every step of the process, workers think in terms of the number of good circuits, not the number of wafers they can move through the line. In effect each team is responsible for its own quality control.
The second step in the work design was to analyze the technical process involved in producing good circuits. To do this, "variance control analysis" was carried out to discover what factors could destroy or reduce the opportunity for each circuit chip to be considered "good". As a result, 120 significant variances were identified. For example, a wafer might not be perfectly flat, or it might not have the proper thickness of film deposits, or the circuit designs might not be perfectly aligned n the wafer/ IT was founds that in the process of building the "gate structure") basic element in microprocessors, and part of the numerous transistors comprising them) alone, there are 15 different things that can go wrong.
Ways had to be developed fir these 120 variances to be controlled. The variances could be grouped into 10 logical units, designed "unit operations" or stat-change units because they constituted identifiable changes in the circuits as they progressed from raw silicon to finished "chips". For instance, the photolithographic impressions of the circuit designs upon an oxide layer of a silicon wafer changed the state of the evolving circuits on that wafer, but the alignment of those circuit impressions on eh wafer does not.
The third step involved designing a social organization (including the division of labor, the design of jobs and the location of internal departmental boundaries) both to match the needs of people who would staff the organization and to control the key technical variances described above. The social organization was to guide the limits of authority, of standards for co-operation and of roes for co-ordination. It was based on a clearly articulated set of values and beliefs about people; in the plant start-up, the premise was accepted that all employees are trustworthy that they can lean and grow, that they can accept responsibility for their product and that they can work together in harmony. He organizational structure described below was designed on the basis of these values and beliefs.
2.3.3 The design structure
The system is based on a philosophy of organizing around a set of results rather than activities. In addition, the integration of people with technology and the involvement of those who build the product with identifying and solving potential problems and with setting goals, are central to the system.
Initially, 23 employees of the company went to Nampa to set o the plant, representing engineering, management, purchasing and materials control. Except for management and the training group, few had operating skill in manufacturing. They see about hiring and training local people who had no experience in semiconductor manufacturing. Since November 1979, about 100 manufacturing technicians have bee taken on. There are currently a total of 146 employees in the plant.
Originally, when the plant was small and growing, and only one product was being built, the production, process was organized in to four work teams of manufacturing technicians, each team with its one manager. Some six to eight months after start-up, other products (similar in process, but differing in execution from the original product) were added to production; and the number of manufacturing technicians in each of the four teams was approaching 25. The management design team, working with the technicians and their team mangers, took that opportunity further to subdivide the four teams into smaller units while retaining the most important "key variance control" within the team structure. The plant now has eight teams of technicians interacting among four work "families" (which correspond to the four original teams).
The plant manager and seven others currently comprise the management structure, which is flat, with two levels above the manufacturing technician. Decisions are made by consensus on the basis of a set of goals. There are still only four team managers, all of whom are part of the original start-up group. These managers focus on development of the eight-team groups and on the problem-solving process. They are involved with helping technicians understand their roles.
In the new plant, employees are taught the manufacturing process from beginning to end, so that they know why they are there. Efficiency is not measured in wafers per hour, but rather in "die" or "chip" costs. In fact, the plant manager prefers to call the plant a "Die generation" rather than a "wafer fab" facility.
The team of employees assigned to a given unit of production has control over all technical variances affecting the "dies", and which are associated with that unit. Such process monitoring is not new in itself. However, in the past in this industry it has not been carried out by the workers building the product, i.e. the people in the best position to solve problems connected with it. Process-monitoring data has traditionally been used by those higher up the organization al ladder, who seldom, if ever, returned feedback.
Plant start-up began with building the social part of the socio-technical design. The key to this was that each work team became responsible for building an identifiable part of the product. The team became truly accountable, in terms of cost and quality, for the successful completion of a state change. To give a team this kind of accountability required a major simplification in organization structure. A conventional "wafer fab" organization (as described earlier) contains highly specialized operators for diffusion and photolithography who communicate not among themselves but through higher-level intermediaries, the engineers and supervisors. If the new plant were to be structures in this conventional way, every wafer would have to change hands 43 times. There would be no way to pinpoint who was responsible for building the product at any point, with the justifiable result that no one would care.
The socio-technical design permitted the structuring of the circuit-building process so that only eight transfers of product responsibility take place. A sense of ownership is achieved because each of the eight state changes that happen to the product is larger and important enough to warrant this. Each of the four work team "families" is responsible for two state changes, and for the quality, quantity and cost of its output. Thus each team has concrete, tangible goal to achieved, Because these team goals can be so easily identified, individual productivity ceases to be an issue for its own sake. However, as part of the team contribution, individual productivity is of paramount importance.
Central to this concept of team work groups is team decision-making. Decisions are not made by managers and handed down to the team to implement. Instead, each team member is fully involved in the decision-making process and understands the reasons behind the decision. The team's level of decision-making grows as the team's knowledge and expertise grow to meet the demands of the tasks it faces.
It had been said that this "decision by consensus" is much more time consuming that decision-making imposed by management. This may be true, but at the new plant it is also proving to be more effective. Even if everyone does not agree with a decision, each worker has had a chance to influence that decision and is prepared to support it. And more importantly, once a decision is reached, its implementation is very rapid. There is no need to communicate that decision three or four levels down the ladder, and there is no questioning of why the decision was made. At the same time, there is no blame attributed to a higher-level authority for an unpopular decision.
2.3.4 The technicians and their teams
The manufacturing technicians, as the operators are called, are organized into teams, each of which is responsible for building a segment of the product. All the technicians understand the entire process and perform a variety of functions aimed at carrying the product through to the next stage.
Acquiring enough information and skill to be an effectible team member obviously requires a much broader level of training than what is usually given to a "fab operator". Every worker must be knowledgeable not just in a narrow task, but in the technical system as a whole, so that the consequences of individual actions can be understood. This is achieved by a two-week (80 -hour) initial training and product orientation course given to all new employees (not just manufacturing technicians), based on the concept that the entire plant has a hand in building good circuits: dies". Over the two years the plant has operated so far, this training course has not been shortened in length or reduced in its content.
The manufacturing teams are deeply involved in analysis what can go wrong in the fabrication process and in solving such problems, so that quality is built in throughout the procedure. In fact, there is no quality control organization but an entire plant focuses on quality improvement. The teams are responsible for making it the tasks of a supervisor in a traditional set-up: they hire, train and discipline their members.
In the first two months, there were over 4,000 applicants for entry-level positions, and the screening process was a considerable task. Once formed, the teams themselves began to help with the screening process as well as selection. Once a team makes the decision to employ someone, it is committed to making sure that the individual is an effective team member. The commitment was evidenced from the very beginning.
The teams manage their own hours. Goals are set for the week and the month, and the work hours needed to accomplish them are planned accordingly. Typically, the equipment is operated by each team for 18 hours out of every 24. In addition, the teams are involved in budgeting, forecasting and even salary decisions. Salaries are competitive in the area. The original salary system was a fixed salary scale based on development of skill and knowledge, and there is a qualification process. The team itself decides on increases for its members.
Figure 35 presents the tasks and responsibilities of team members, and of management. At regular goal-setting meetings, the team determines what it needs to do during the week to achieve the required quality, quantity and cost levels. Team members decide among themselves how many hours they will need to work that week, which variances they have to watch out for and what personnel problems they have to tackle. The team's authority extends to screening and hiring new members when it needs them, as well as managing individual performance of its members.
What is management's role in all this? Often the plant manager knows very little of what is going on in any given team; and this is to consider a necessity. The role of management is to provide the teams with enough information do that they can set reasonable, compatible goals. Because the team members have the information and skills to achieve those goals, they are trusted to make the decisions on how to achieve them.
Clearly, demands are often made upon the team from external sources e.g. from organizations outside the company or even other teams. It is management's task to interpret and clarify these demands for the team. This is known as "boundary management", i.e. defining where the team's responsibilities begin and end, and what is expected of members both inside and outsides the team group. Management tasks and responsibilities outside of those of the teams are shown in figure 35.
One essential ingredient for success was that plant management entered this process fully committed to, and supportive of the design team idea. In spite of skepticism from outsiders, the experiment so far appears to be working. We give some examples below.
At one time or another, every company in the industry has faced problems connected with the process of growing intermediate oxides on silicon wafers. Their susceptibility to poor visual quality can lead to low-quality yields during the subsequent photolithographic process. In addition, temperature shock occurring when the wafers are removed from the heated chamber of the diffusion furnaces can cause breakage levels higher than desired. At the new plant these problems were addressed totally by the teams responsible for this phase of the manufacturing process. The team members worked together to come up with a solution to a problem that had long plagued the company's Cupertino plant as well.
Personnel problems are solved in much the same way. There are not time clocks in the plant, but team members monitor each other's contributions. An individual who is not meeting his commitment to the group will first receive verbal feedback from co-workers. If the problem persists, the group will draw up an actual written contract with the individual to change his or her behavior. The team is fully supportive of the member often working with him or her to identify the problem and find a solution.
We cannot go into detail here about the preventive maintenance programs, and even equipment changes that the teams have made. However, we attempt to answer two key questions: Did the teams achieved the goals set for the new plant and, even more important, have these achievements been maintained after two or three years of operation?
2.3.5 Results
Good results seem to support this approach. Table 91 shows actual results. The plant has lost six operators and three managers in it two years of operation, a less than 6 percent annual turnover. The typical rate for "Silicon Valley" fabrication plants for the same period was 55-60 percent. Sometimes, as in mid-1979, when the industry was booming, turnover rates sometimes peaked at 100 percent or more. Fabrication plants outside the "Valley" have been known to have turnover this high, although in the average it is generally slightly lower than these figures. Turnover rates at the remote plants of other companies are low, but not as low as at the Nampa plant. This low attraction rate is translated into higher performance and greater efficiency, as well as cost savings, given the time taken for an operator to become proficient.
The pant saw its cost go down after manufacturing began in the fourth quarter of 1979. Output was increased to the point where the pant was serving its customers and obtaining a satisfactory return in investment by early 1980. Since the start-up time was cut by half, the investment cost, which is closely related to how quickly a plant comes up to standard, was also reduced proportionally.
A dramatic increase in product quality yield has been achieved as compared with experience of the company in "Silicon Valley", and with reports of yields at other companies. Yields at the new plant exceed those of comparable facilities by more than 25 percent it thus performs well above the industry average as cited by independent research organizations. Success, however, is not only measures in yields; the teams approach has reduced the amount of reworking, and therefore also the cost of labor.
2.4 The current situation: problems and prospects
The plant is geared to high-volume "chips", and is currently set up for two basic processes: one for most logic products and microprocessors, and the other fro memories.
The biggest problem in making the system work was within the management team. It was difficult to shed the traditional management roles where boundaries are clearly defined, and to make a commitment to a new philosophy. The plant management team has to solve the problem of how to interact with the outside world and to translate exterior demands (i.e. the company's Cupertino plant and customers)/ Management's roles, too, was to teach. According to the plant manager, "we are obliged to clarify what's expected and why, and we leave the freedom on how o do it up to the teams". "It took three months to a yeas before the managers felt comfortable", he continued. "IT was particularly difficult at first to stand back and let the teams decide how they were going to solve problems. Nevertheless, when the results started coming in, everyone relaxed. " Only one manager so far has been unable to adjust. He was hired as personnel manager and found the lack of restrictive rules, such as attendance requirements and set hours, difficult to contend with.
Recently, as the plant moved into its third year of operation, the following question was asked of members of the organization: To what do they attribute their success and feel are necessary ingredients for continued improvements? The principle discussed below highlight critical factors.
First on the list was corporate support. With out the initial and continued support and willingness to risk doing something new with the design of a new plan from the president and group Vice- president of Operation, the results might have been very different. This new manufacturing plant was the company's first domestic expansion effort, and it would be the home for future growth. This new method of organization design (never before tried in the semiconductor industry) was no easy decision with a new plant and new equipment, 700 miles from the technology base, as well as new employees, new technologies and products soon to be delivered.
The second factor was the management commitment of the initial site members who made up the Nampa design team. They seemed to be convinced that there must be a better way of managing and operating a manufacturing facility. This fact helped them to overcome the many problems and unanswered questions that accompany new plant start-ups. Soon after these new managers were hired, they attended a weeklong workshop on open systems design theory and team building. This workshop was attended by both those allocated to the new plant and key company personnel, including the President. This workshop helped the design team to begin to come together as a real management team with a vision of " something different".
Workshops played an important part in the overall development of the plant. Soon after the initial 40 or so individuals were gathered at the site, all members of the plant participated in a weeklong workshop to explain the design technologies to be utilized and to encourage team building. This was an experimental workshop attended by manual workers as well as mangers and professionals, and followed up by numerous workshops, team-building sessions and external innovative plant visits by members of the plant.
The next area mentioned was that of design technology. The methodologies of socio-technical systems design, open systems planning, general system theory and transition planning were all extremely useful in the overall plant organization design.
Somehow, the geographical separation of 700 miles from corporate head-quarters and other departments in the division was mentioned as helping the new plant pull together as a team internally and utilize the strength and expertise that existed in the plant.
Other areas mentioned as important to the success of the plant include the felt need or pressure because of the business requirements to design and operate a high-quality plant in term of product and working life. The felt need was no accident, but grew from an important early decision to initiates and to emphasize statements of mission and philosophy. The mission of the organization, to "build high-quality dies (electrically good integrated circuits) at minimum economic and social cost". Distinguished the plant as one that manufactures quality products as opposed to one that merely "moves material". This then led easily to identifiable goals for the plant. The statement of the mission, and the objective focus of the design team on a statement of philosophy about organizational values and benefits, together made a powerful and visible keystone upon which the organization could operate.
Also mentioned as essential to the success of the organization was the importance of communication, clarity of expectations and openness about the goals of the organization. This candor, along with open office space, facilitated the openness and trust that bonded the organization together. It seemed that communication was a key element that began breaking down traditional barriers between departments and helped to foster trust throughout the organization.
Instead of the syndrome that exists elsewhere in the semiconductor industry, where on individual stands out as taking all the risk and consequences of a decision, the system on the new plant emphasizes the importance of consensus decision-making and good technical resources, where expertise is pooled together to help solve challenges the organization may face. Consensus risk-taking, where key parts of the organization, which were knowledgeable, were brought into taking the necessary risks, required a high-performance organization.
"Ego death" was one of the key elements that most of the managers felt was an important factor which helped facilitate the growth and development of the organization as a whole. This refers to a change from traditional management beliefs that decision-making, risk-taking and being recognized as the unique expert are the primary sources of management pride and satisfaction. When managers foster skill development, information flow, decision-making and risk-taking at lower levels in the organization, they learn that devolution derives a team reward in which they share and from which their satisfaction is enhanced.
Some other areas mentioned as responsible fro success were the importance of a good selection process, orientation and assimilation process, which are managed by the teams with whom a potential organization member would work. The teams are involved completely in the interview and selection process and with the orientation and planned assimilation program, along with their new members, Although a large available labor pool has offered selection ratios as high as one technician selected for every 40 applicants, the selection criteria have remained simple - good vision, an interest in other people and a willingness to try something new. Flexibility, adaptability, patience and the ability to deal with ambiguity are all important characteristics that the organization has found to be essential.
Three areas where much more work will be needed in future expansions at the site (and which are felt to be necessary for high performance) are manufacturing, equipment and plant layout prior to construction of the total building, social preparation (to prevent culture shock), especially when moving from the San Francisco bay area, and integration and clarification of expectation with corporate and other external company y members upon whom plant employees depend, and who depend upon and use the plant's products and resources.
The new plant operation has been a model fro making some changes in the Cupertino manufacturing operation that have resulted in lower costs. The company is also in the process of implementing a socio-technical approach in several non-manufacturing departments in Cupertino. Since no two designs are alike and a redesign is more difficult than a design from start-up, the current projects bear little resemblance to the start-up described in this case study. It was emphasized by the company President that the Nampa design could not be imposed on other plants, simply because it had worked in that particular case. Ownership could only be created if people believed in what they were doing, and were able to take the initiative themselves. Nevertheless, since the Cupertino plant wanted to implement a redesign, the company supported the move. Since the design process has started, both the President and the Nampa plant managers agreed that the resulting organization for the Cupertino plant will probably be quite different from the Nampa structure because of the differences in the needs of the technical systems, the people and the external environment.
Notes: United State Department of Labor, Bureau of Labor Statistics: "Current Labor Statistics", in Monthly Labor Review, Nov. 1981. pp. 61-99. Howard Fullerton, Jr. : "The 1995 labor force: A first look", ibid., Dec. 1980, pp. 11-21.